The longer the ride distance or greater the overall cycling volume, the more critical the touchpoints on a bicycle are. Gender, body dimensions and shape, rider flexibility, specific riding postures, and other highly individual factors make having the perfect fit at the handlebars, pedals, and saddle difficult. Throw in personal preference, and the optimal fit seems like a minuscule target.
Of the three contact points on the bicycle, the seat is the most problematic for most. Saddles have improved tremendously in the 4 decades I’ve been spinning pedals. The now-common cutout in the middle of the seat was a vast improvement, as was the recent move to 3D-printed padding.
Today, Fizik announces what could be the next significant advancement in saddle comfort. The Italian brand launches the One-to-One program, which utilizes pressure mapping to create a true bespoke custom saddle.
How fizik One-to-One Works
The fizik One-to-One process starts at a select dealership. The cyclist is given a personalized measurement session to determine which of the eight fizik Adaptive saddles is the most suitable. This selection is primarily based on the overall saddle shape.
The next step is probably the most crucial. A pressure mapping session that measures 64 saddle touchpoints on the current saddle and the chosen Adaptive saddle identifies peak pressure hotspots, instabilities, and asymmetries while pedaling.
The fitter measures these parameters with different riding positions based on the cycling discipline. For example, for road bikes, measurements are taken with hands on the tops, brake hoods, and drops.
The pressure mapping is done through a gebioMized saddle cover that houses sensors that report this data to a computer. This technology is also used by very high-end bike fitting services.
This data is captured and analyzed, and a truly custom, one-off 3D padding structure is designed to match the cyclist’s needs, as determined by the pressure mapping. The customer then chooses the saddle rail material they want (carbon or Kium), and the order is sent to fizik’s headquarters in northern Italy. Once the bespoke saddle is built, it’s sent directly to the customer.
The customer returns to the fizik dealer for another session to record pressure data again. This final step highlights the improved measurement parameters. The fizik One-to-One is not the first custom-printed saddle, but it is among the first to utilize pressure mapping.
How Do I Get One?
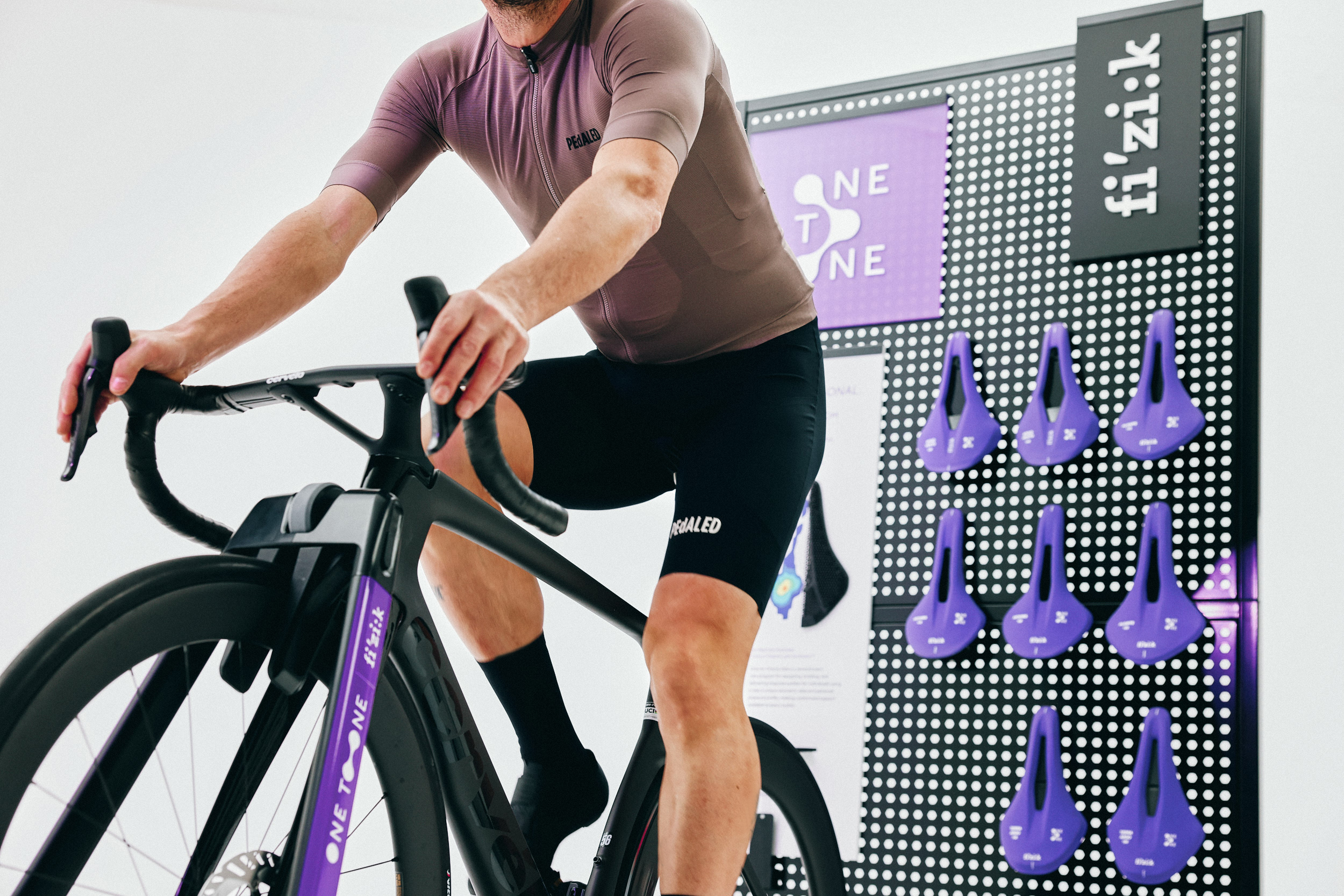
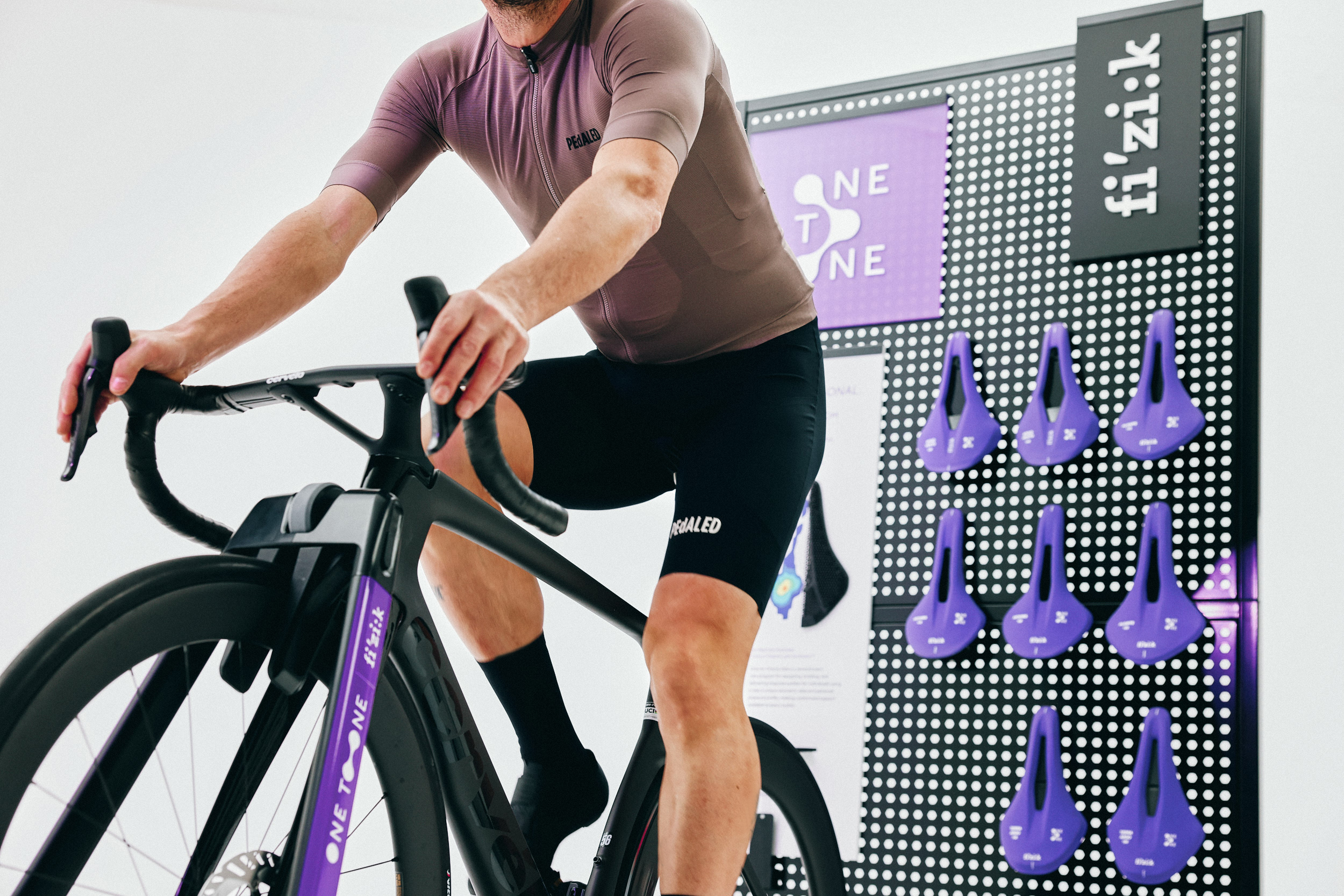
The first step is to determine the nearest fizik dealer that offers the One-to-One program; refer to this list. The select dealer will execute the process from there, and in approximately 2 weeks, your custom 3D-printed saddle should arrive on your doorstep. After mounting, all that is left is to return to the dealer for the final pressure mapping session.
Of course, something like this isn’t cheap. fizik One-to-One Adaptive saddles start at an MSRP of $499. But, keep in mind that some off-the-shelf fizik saddles have an MSRP of $400. Yes, that is a lot of money, regardless. But the saddle on a bicycle is a huge contributor to overall comfort and enjoyment, and you’ve exhausted every other option. then this may be a solution. And saddles tend to last a long time.
The Future of 3D Printing in Cycling
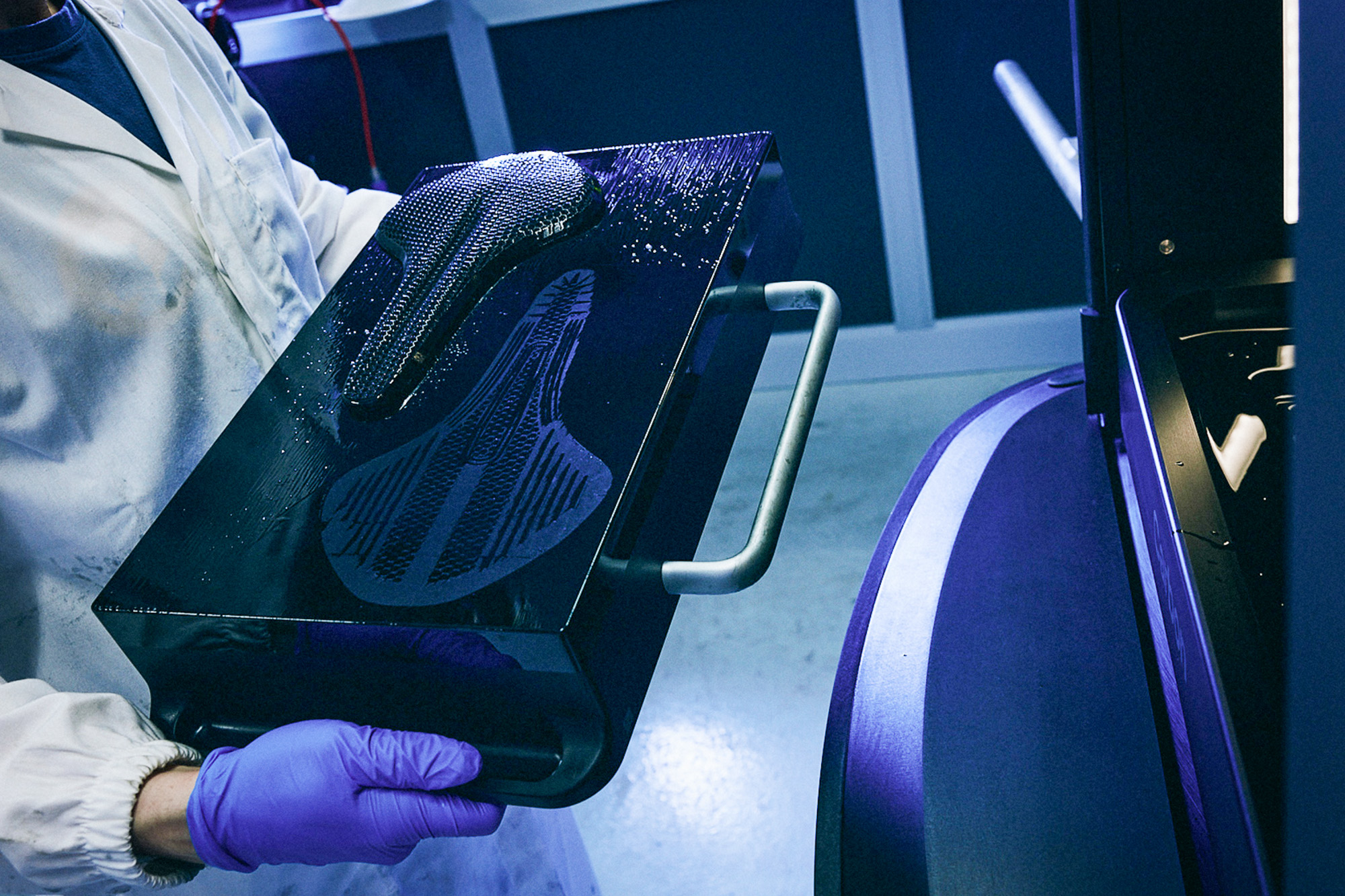
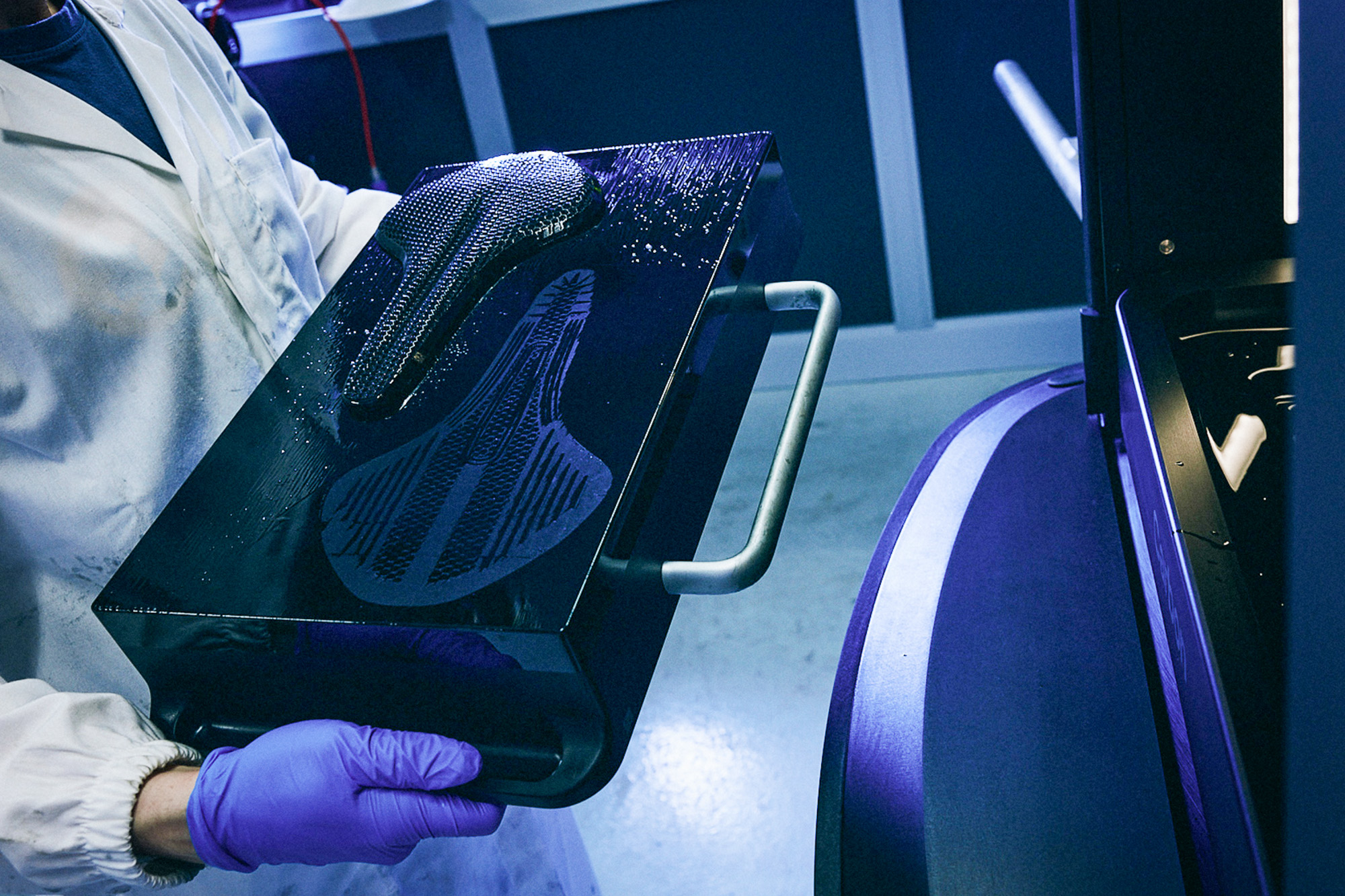
I’ve been on stock 3D-printed saddles for a few years now, and I have to absolutely admit that they are super-comfortable and supportive at the same time. The ability to modulate the span from pillowy cushioning to firm support via 3D printing overcomes many of the limitations of foam in classic saddle manufacturing.
I predict 3D printing will enhance the other touchpoints on a bicycle. The shoe/pedal interface and the glove/handlebar juncture are places where I can see 3D printing technology improving both comfort and support. And indeed, I recently received notice of 3D printed handlebar tape.
Bicycles have always been a platform for brands to flex their technological chops. Most of it is centered on making the rider faster. And at times, these efforts sacrifice comfort for speed. But fizik One-to-One is refreshing as it’s aimed squarely at improving comfort and enjoyment. Which, in the end, may improve speed.