We may earn revenue from the products available on this page and participate in affiliate programs. Learn More ›
This is the first in a two-part installment on the Nightforce ELR Steel Challenge.
The Nightforce ELR Steel Challenge is arguably the most difficult long-range match in the world. It is held each year on a large ranch near Glenrock, Wyoming. Competitors come from all over the globe for the opportunity to pit their skills against each other and the demanding course of fire, which consists of steel targets arrayed from 800 yards out beyond 2,000.
It’s safe to say that the skill set of the assembled collection of shooters is unrivaled—at least as far as long-range shooting at steel under practical field conditions goes. And yet, the majority of the 300 shooters who participated head home after the two-day ordeal feeling beat to a pulp by the experience.
Simply put, the competition is brutally unforgiving. If there’s any weakness in your gear, load development, marksmanship skills, trajectory calculations, wind calling, load development, or mental focus, this match will expose and exploit it to your detriment. It’s a meat grinder, but that’s part of its appeal.
Proper Preparation Prevents Piss-Poor Performing PRCs
While you won’t win this match through preparation alone, it is certain that you will lose—and badly—if you don’t put your time in before the range goes hot that first morning.
Every high-level shooting competition requires a degree of prep, but with matches as demanding as the Nightforce ELR Steel Challenge it takes on an extra level of urgency.
The following is a rundown of what I did in the weeks and months prior to making the 450-mile drive from my home to Glenrock.
Team Effort
Even though I’d be shooting the match as an individual, during the preparation process I worked closely with a group of friends who I planned to squad with. This included Scott Seigmund, the vice president of Accuracy International of North America, some of Scott’s AI team shooters I’ve come to know over the years, and two of my buddies from Montana—Chris Gittings and Owen Koeppen who were competing in the team division. Shawn Burkholder, the owner of Hawk Hill Custom Barrels, also joined our crew.
.300 PRC Bandwagon
Scott and his boys shot .300 PRCs the year prior and had good success with that round so Chris, Owen, and I decided to shoot it as well. In previous Nightforce ELR matches Chris shot 6.5s (both the 6.5 SAUM and 6.5 PRC) and had several podium finishes.
But the consensus was that the .30-cal magnums—the .300 Norma Mag., .300 PRC and some .300 Win. Mags.—had an edge over the 6.5s at the location where the match is currently held.
The two main reasons for this are the high winds at the ranch—it is smack dab in the middle of a wind farm—and the thick sagebrush cover that dominates the landscape. The big .30-cal bullets handle the wind better than the 6.5s, while the sagebrush makes it more difficult to spot misses. The smaller 6.5s get eaten up by the foliage more readily than the harder-hitting .30s.
Cartridge Components
Not only were we all shooting the .300 PRC, but we planned to all use the same components for our handloads, which we acquired in bulk. Our bullet of choice was Hornady’s 230-grain A-Tip, which is one of the best .308-caliber match bullets on the market. It is blessed with a high BC (.823 G1, .414 G7) and like other A-Tips it is manufactured to exacting tolerances to minimize variations from one projectile to the next.
ADG Brass
For brass, we turned to Atlas Development Group, which makes excellent high-quality cases. I’ve used ADG brass many times over the years, including in my ultimate open-country rifle build, and have had nothing but excellent results.
AI AXSR Chassis Rifle and Hawk Hill Customs Barrel
Most everyone on the squad was shooting Accuracy International AXSRs, which are among the best sniper rifles currently fielded by military and law enforcement and are one of the most accurate rifles period. Scott got us lined up with barrels from Hawk Hill Customs. With a 1:9 twist, those 30-inch barrels had no problems propelling the 230s at 3000 fps.
But as you’ve no doubt heard, just because you can do something doesn’t mean you should. Running cartridges full tilt is a risky proposition in a high-volume long-range match. Performance tends to get more inconsistent at the ragged edge of maximum velocities and the chances of getting a case stuck, blowing a primer, or experiencing some other calamities go way up.
Instead, we all set a target velocity of 2940 fps, which is more than respectable and would keep our bullets supersonic well past 2,000 yards in the thin Wyoming air, but which was also mild enough to diminish the chance of some mid-stage mishap.
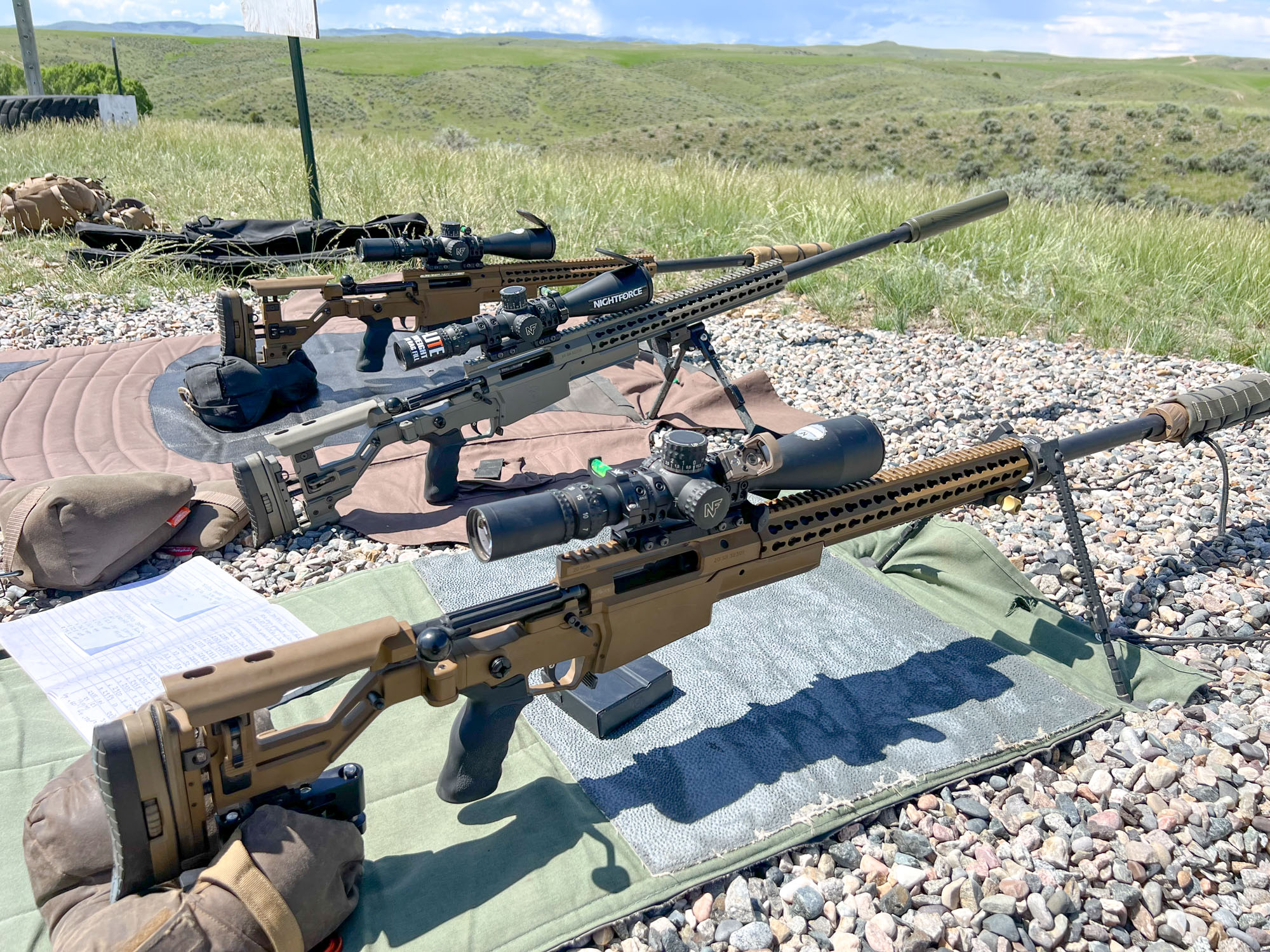
Hodgdon H1000 Powder
I helped secure 64 pounds of the same lot of H1000 for our group. I’ll tell you what, I was feeling a little cocky about that coup. That powder, one of the mainstays for long-range magnums, has been unobtainium since the global pandemic.
All of us running the same cartridge using the same batch of bullets, the same type of brass, and the same lot of powder—at the same speed no less—was going to make our collective load development a snap and give us an edge over much of the field. As I’ll get to in a bit, it turns out my celebratory cork-popping was premature.
Gun Prep
Whether you’re getting ready for deer season or prepping for a big match, it makes sense to go over your gear with a fine-toothed comb—particularly your rifle and scope.
I had been shooting my AXSR a fair bit in the months prior to the match, leveraging its multi-caliber capabilities to test 6.5 PRC and 7 PRC ammunition. Even so, I stripped it down, gave all the fasteners and components a thorough cleaning and inspection and reassembled it.
To make sure my scope—a Nightforce ATACR 7-35×56 with the Mil-XT reticle—was dead nuts level in its Spuhr mount, I used a Short Action Customs’ Final Scope Level and Accessory Kit.
That SAC scope level has been a game changer for me. When shooting at extreme long range, even the slightest cant in the reticle will throw your trajectory off. In conjunction with the plumb line in the accessory kit, the leveling base lets you set the orientation of the reticle so that it is perfectly vertical.
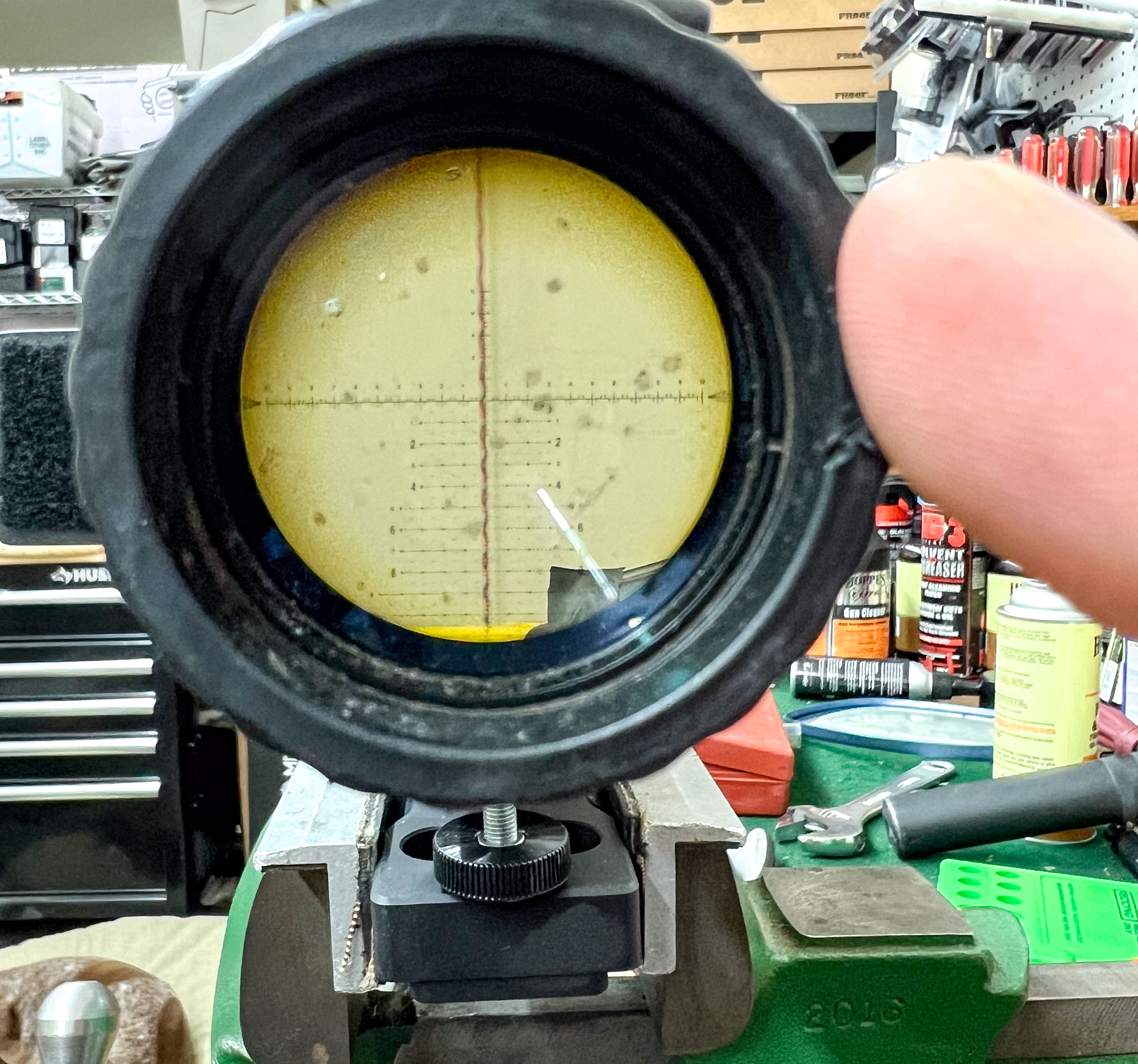
Barrel Break-In
Before I got down to the serious business of load development, I needed to break in my new barrel. There are numerous schools of thought about how to break in a barrel, or whether it even makes a difference.
For most applications, particularly with hunting rifles and rifles that will be shot mostly within 1,000 yards, I’m skeptical about the benefits of an ornate break-in procedure. But there’s no doubt that a barrel will speed up after a certain number of rounds and making sure it has stabilized its velocities is critical for generating precise ballistic calculations.
In light of that, I decided to follow Scott Seigmund’s recommendation, which was to break in the barrel over the course of the first 100 rounds. Here’s his method:
- Shoot five rounds and clean (repeat four times for 20 rounds total; cleaning procedure below)
- Shoot 10 rounds and clean (repeat four times, bringing the round count to 60)
- Shoot 20 rounds and clean (repeat twice, for a total of 100 rounds)
Velocity Gain
I shot factory Hornady 212-grain ELD-X ammunition during the break in. The first 30 shots were consistent, averaging 2920 fps. Then the barrel sped up. I chronographed the next three groups of 10 shots at 2935, 2938 and 2939 fps, for an average of 2937 fps. I got another bump with the next 40 shots, where the barrel sped up to 2952 fps.
I was 100 shots into the process, but didn’t feel my barrel had totally settled in. So, I shot two more 10-shot groups and recorded an average velocity of 2965 fps. At this point, the barrel had gained 45 fps.
I needed to start developing my load for the match since my time was limited, but every time I cleaned the barrel during that process I’d shoot more of the factory ammo, which was all from the same case, to see if the barrel picked up more speed.
When all was said and done, that factory ammo shot 3004 fps on average, for a total velocity gain of 84 fps.
Cleaning Procedure
When it was time to clean, I removed my Thunder Beast 338 Ultra SR suppressor and unscrewed the barrel from the chassis. That’s accomplished by loosening a 4mm set screw on the side of the chassis and then using a 1-inch wrench that fits in the flats machined in the barrel a couple inches below the muzzle.
Being able to pull the barrel so easily made cleaning a snap. I’d spray some Hoppe’s Elite down the bore and then push a couple wet patches with my .30-caliber jag and cleaning rod. After letting that soak for a few minutes, I’d switch to a rod with a copper brush and give it 10 strokes back and forth. (When using a brush, always wet the bristles with solvent first.)
After that I’d run three wet patches through the barrel. The first one would be filthier than a USMC Sergeant’s mouth while inspecting his platoon. The second is always moderately dirty. And the third should be more or less clean.
At this point you have a decision to make. The fouling from the powder has all been removed, as has most of the copper. But if you want to really get as much copper out of the bore as possible (I did), let the barrel sit for a while so the solvent can really work. Wait at least five minutes (10 to 15 minutes is even better) and run another wet patch down the bore. If the patch comes out bright blue, it means you’re still removing copper. Repeat this process until the patch only has a hint of blue. (FYI, since many jags are brass, which contains copper, you’ll get some blue on your patch no matter how little copper remains in the bore.)
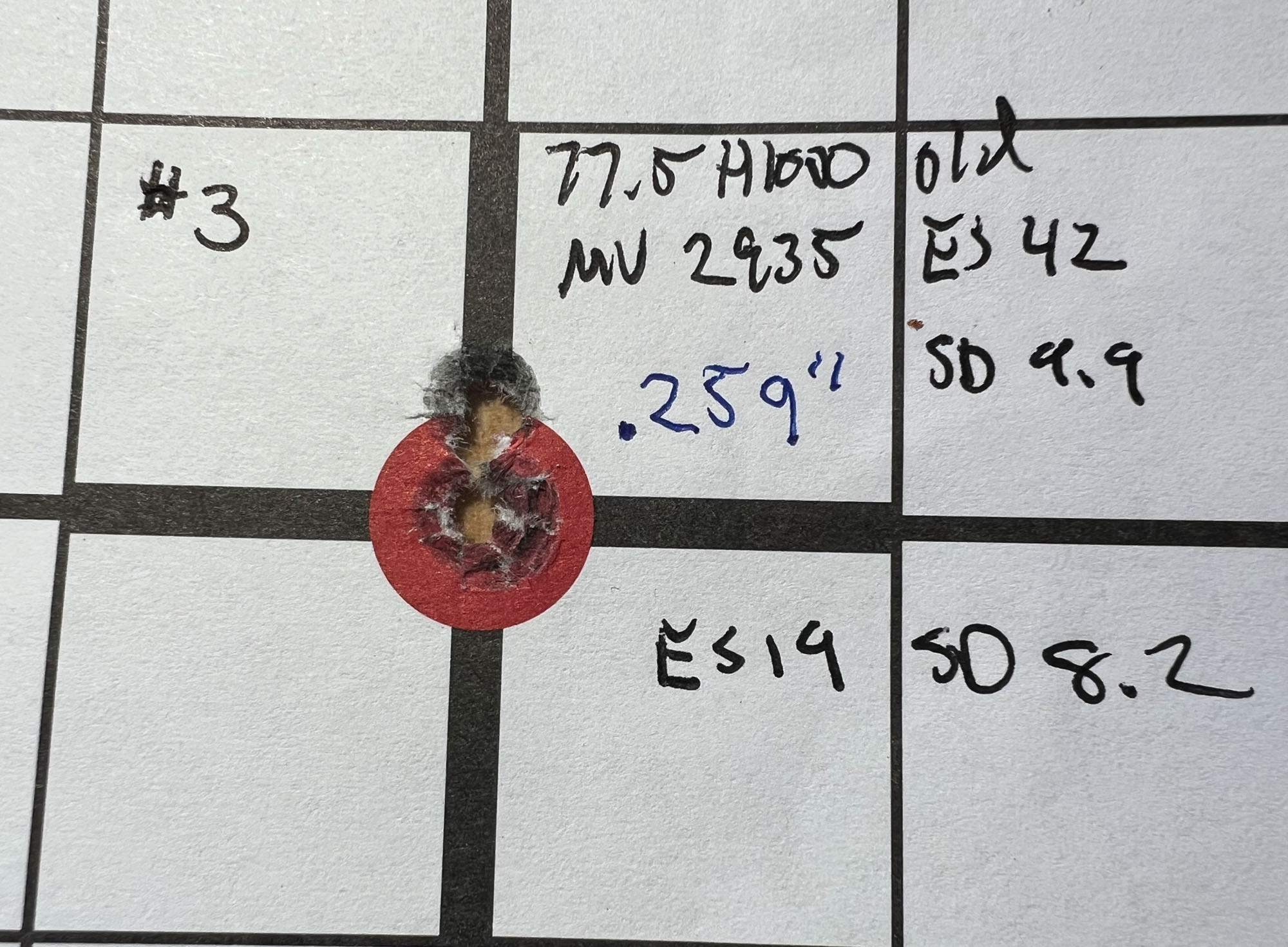
Accuracy Gain
During break in, I also measured every group the factory ammo produced. I started by shooting and measuring five-shot groups (since that was the cleaning interval), but then switched to 10-shot groups, which is a better representation of the rifle’s performance. It’s also in keeping with the round counts during the match, where you might shoot up to eight rounds a stage.
I wasn’t expecting magic at this point since those groups were all shot from a cold, thoroughly cleaned barrel—but I was curious to see how those factory 212 ELD-Xs performed.
The first group through the virgin barrel was an encouraging .773 inches. But the next three groups opened up to 1.210 inches on average.
At this point, I shifted to 10-shot groups. The barrel definitely tightened up. The next 70 shots of 10-shot groups averaged 1.18 inches. Under normal circumstances, going from a 5- to 10-shot group will see a bump in group size of about 25 percent. So the fact that groups with twice as many shots had an average dispersion just as tight, is a good thing.
Then my last three 10-shot groups tightened up even more, averaging .928 inches. Between groups I’d let the barrel cool as long as it needed so that the area around the chamber was barely warm to the touch. At this point I was feeling pretty good.
Consistent Factory Ammo
One thing I noted about that factory Hornady ammo is that it shot consistently in terms of its velocities as well. The standard deviation of those first 120 shots (measured in shot strings that varied in sizes of 5, 10, and 20 rounds) was 14.8. That’s about as good as it gets with factory ammo.
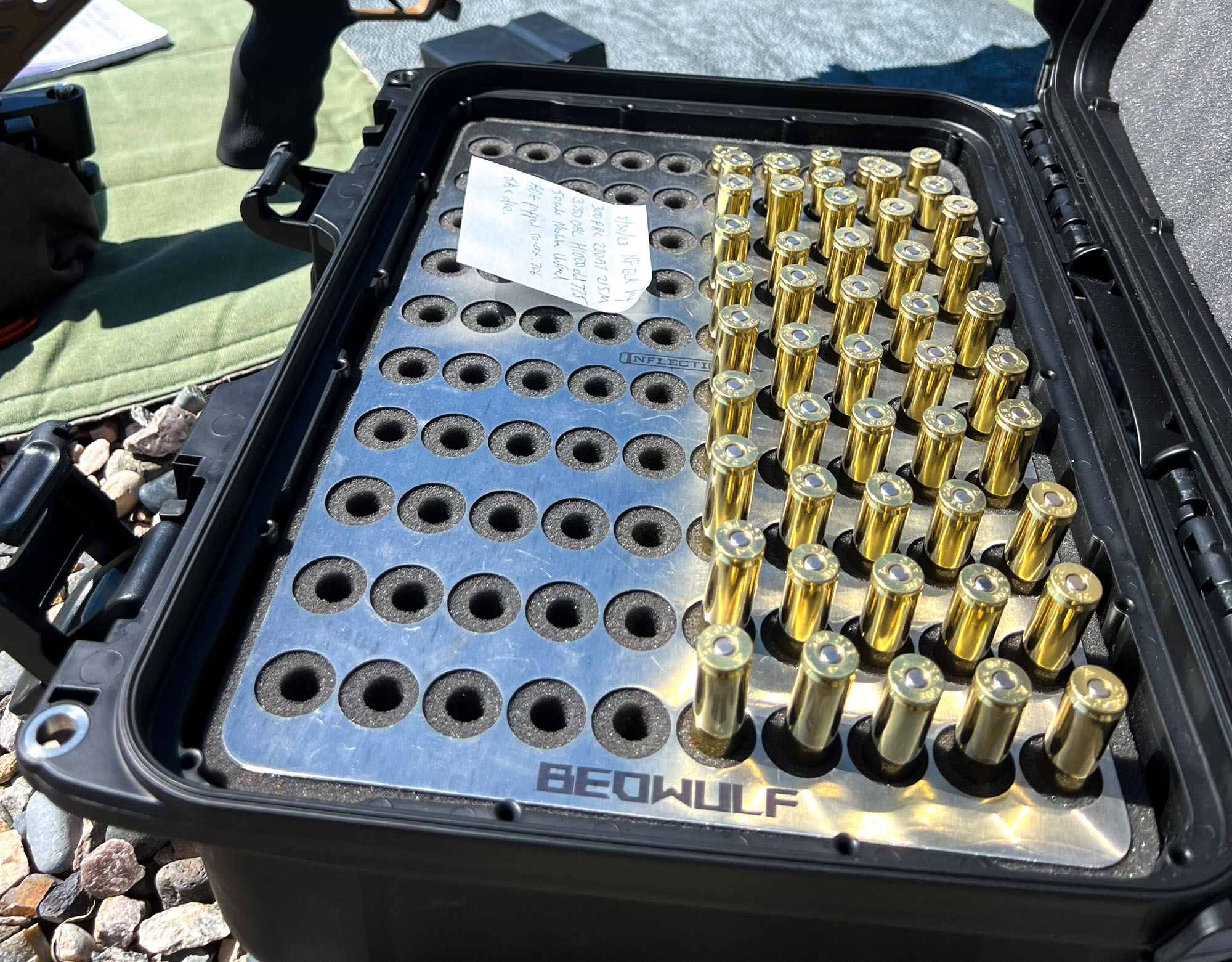
Load Development
My fervent hope whenever developing a load is that it progresses smoothly and quickly toward eye-popping accuracy. I thought the cards were tipped in our collective favor with our .300 PRCs for several reasons. One, Scott and his team shot a similar load the year before with good results. Two, we were all pulling on the same oars by virtue of having identical components. Three, our aggregate experience with long-range shooting and precision handload spans many decades.
With stars in my eyes and hope in my heart I got to work at my reloading bench.
Brass Prep
All brass, no matter how expertly crafted, has a certain amount of variation from one piece to the next. You can see that in neck wall thickness, headspace (most commonly measured from the case head to the mid point on the shoulder on bottle neck centerfire cartridges), overall length, neck diameter, and so on. Necks in particular are susceptible to dings that throw them out of round, so before loading it makes sense to run them through a mandrel to make them uniform and concentric.
After taking my initial measurements on 10 pieces of brass, I ran them through a neck mandrel on my Forster Co-Ax. I then trimmed the brass to a uniform length on a Giraud Power Trimmer, which also chamfers the interior and exterior of the neck.
I was pretty happy with the results, but as my load testing went on I felt there was room for improvement. I added a step of running the new unfired brass (I had 400 pieces total) through a SAC Sizing Die with a .333-inch neck/shoulder bushing.
This uniformed my brass beautifully in terms of neck diameter and shoulder length. A neck diameter of exactly .3335 inches on every case ensured my bullets would be gripped with the same amount of tension, which is critical for peak precision. Uniform shoulder setback is beneficial for consistency too.
Here’s some extra information for those who might care. The degree of constriction on my bullets—meaning the difference between the bullet diameter (.308 inches) and the interior diameter of the neck (.3055 inches)—was .0025 inches. Generally speaking, neck constriction between .002 and .004 inches is a smart bet—so .0025 inches is right on the money. To calculate the interior diameter of the neck you take the exterior diameter—in this case .3335 inches—and subtract twice the neck wall thickness, which on the ADG brass averages .014 inches. So: .3335 inches – .028 inches = .3055 inches.
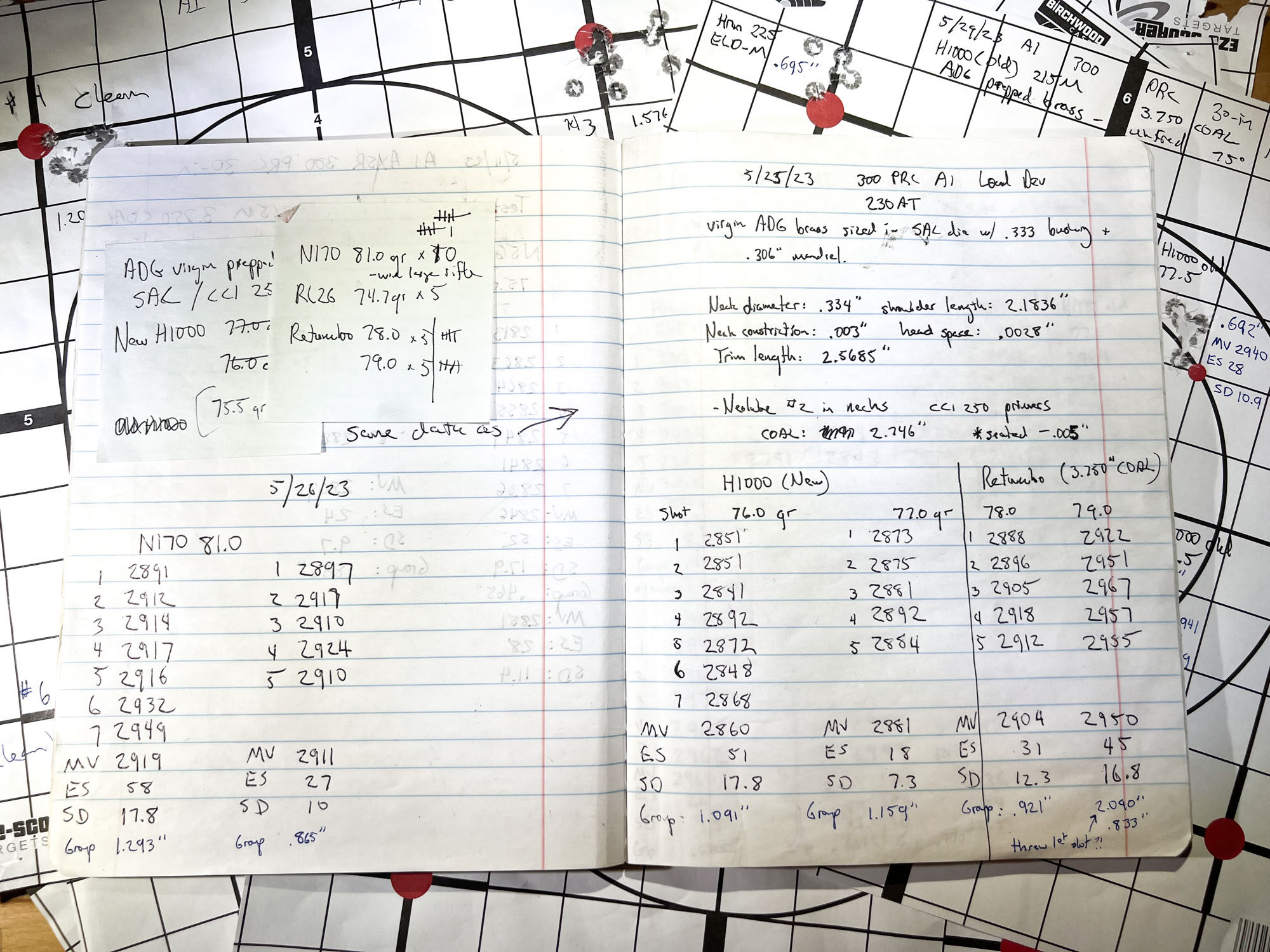
Ladder Testing
There’s a lot of hokum around how to conduct a ladder test and what the significance of it is. The common wisdom is that you shoot small samples of different charge weights and measure their velocities to find flat spots, or “nodes,” in the results. The theory is that a flat spot indicates forgiveness in the charge weight—meaning you can be off in your powder charge by a tenth or two of a grain, and still have similar muzzle velocities.
I have some good news and some bad news here. The bad news is that this theory is a pile of hot garbage. These nodes don’t exist. When reloaders think they’ve come across a node all it really indicates is that their sample size is too small.
Most reloaders will load only a small number of rounds at a given charge weight. Sometimes, that number is as small as one, but rarely does anyone load more than five rounds at each weight. This is done to save time, money, and barrel life.
But for gathering statistically valid data, these sample sizes are insufficient. I’ve done a lot of searching for these nodes with three- and five-shot samples. I noticed that when I repeated the tests multiple times and overlaid the data that the velocities versus charge weight behaved in a linear fashion, the nodes disappeared.
This has been borne out by my friends at Hornady—specifically Jayden Quinlan and Miles Neville—who are two of the company’s chief ballistic nerds. They’ve conducted controlled experiments with massive data sets that show these velocity nodes are a myth.
The good news about nodes is that you don’t need to bother looking for them. Instead, use your ladder test to simply arrive at a target velocity and then start testing for accuracy.
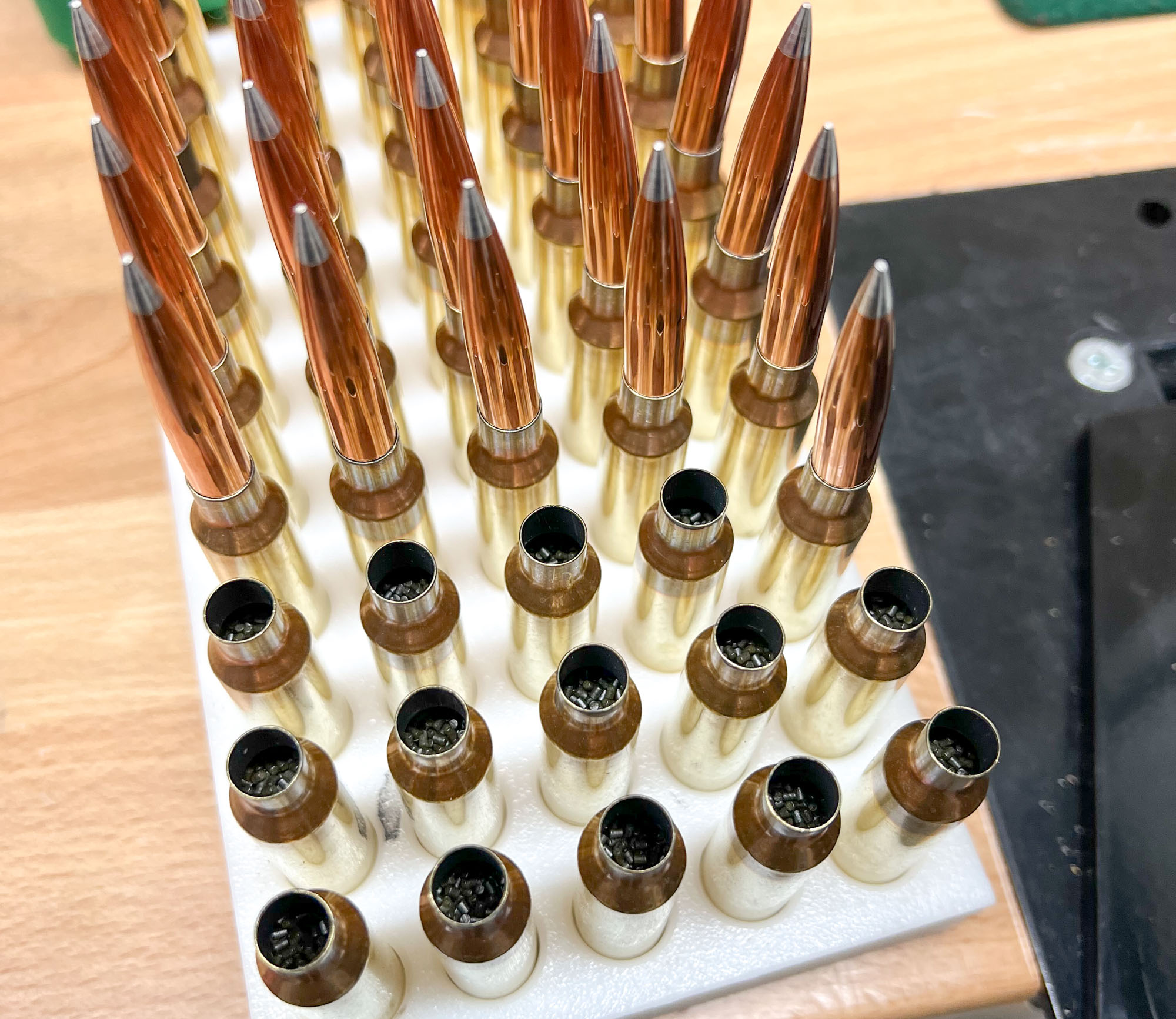
H1000: Old vs. New
My share of the 64 pounds of H1000 we got for the match was an eight-pound container. Because I like to gather data, I wanted to compare this new lot of H1000 against some of my older, pre-pandemic H1000.
I quickly saw there was a bit of a difference in my velocities. The older H1000 was about 25 fps faster per given charge weight than the new stuff. While 76.5 grains of the older lot got me around 2940 fps, it took 77.0 grains of the new H1000 to hit the same speed.
That didn’t concern me much, but the differences in accuracy did. My first efforts with the new H1000 didn’t impress me. I shot three five-shot groups that averaged 1.516 inches, which for this rifle and application is terrible. With the older powder I shot one five-shot group that measured a tidy .590 inches with an SD of 10.3, which was much more encouraging.
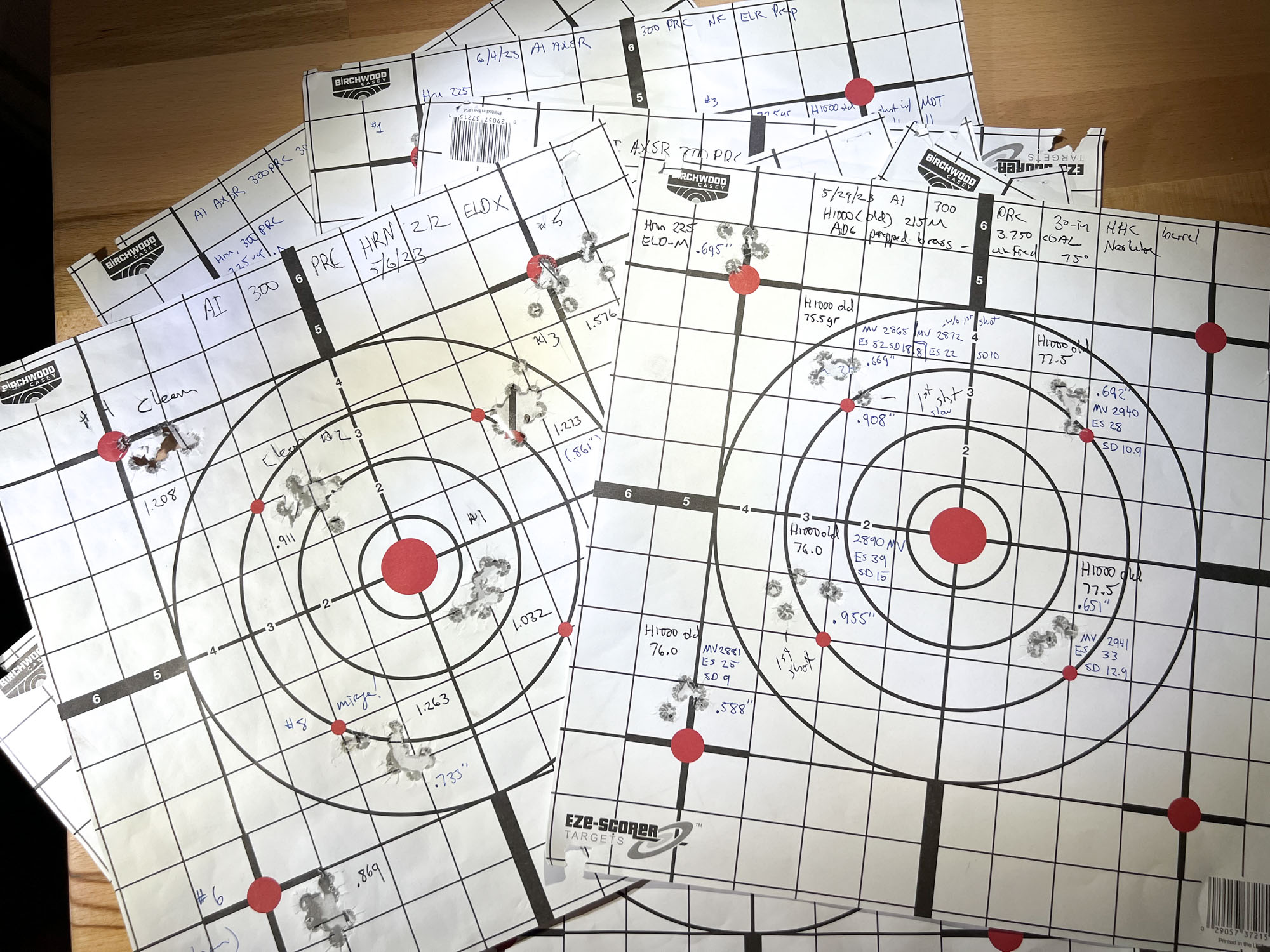
Testing Other Powders
The fact that the new H1000 powder didn’t seem to agree with my rifle and loads threw a monkey wrench into my vision of having our whole team running identical loads. Turns out my squad mates were having similar struggles finding a load that would be competitive in the match.
Some had better results when they switched from Federal 210M primers to CCI 250s. Their velocities got more consistent, and accuracy improved.
I didn’t have that option, as my primer selection was limited to the 210Ms. So I started messing around with other powders. I shot N565, Retumbo, N170, and Reloder 26, as well as more of my old lot of H1000.
I got the best results with N565 (.680-inch average), RL 26 (.710-inch average), and my old H1000 (.648-inch average). That data is based on multiple five-shot groups.
Final Match Load: 77.5 Grains of H1000
Because I had the most data with the old H1000 and had the best results, that’s where I focused my efforts. I was running out of time and needed to finalize the load in order to dial in my ballistic calculations.
I had shot a lot of groups with the older H1000 with charge weights from 72.9 grains to 78.0 grains. Across that broad range of velocities—which varied from 2775 fps to 2960 fps—my groups averaged the .648 inches, as mentioned above, and my SDs were right at 10.9.
Within that range I seemed to have better results between 76.0 grains and 78.0. At 78.0 grains the load was running a little hotter (2960 fps) than I cared for. But when I knocked .5 grains off that charge, I landed right at 2940 fps and everything tightened up. I shot six five-shot groups to confirm. The averages of my groups (.540 inches) and SDs (9.3) would be competitive.
It’s worth noting that during my struggles to find a good powder and powder charge, I burned through a lot of ammunition and spent a lot of time making the hour round-trip drive to my gun range. All told, the barrel break-in and the load development required 373 rounds to complete. That’s a good chunk of my 30-inch Hawk Hill’s barrel life, which based on how I run it should deliver peak performance for 1,600 rounds. I liked where I ended up, but I’ve never worked quite so hard to develop a load.
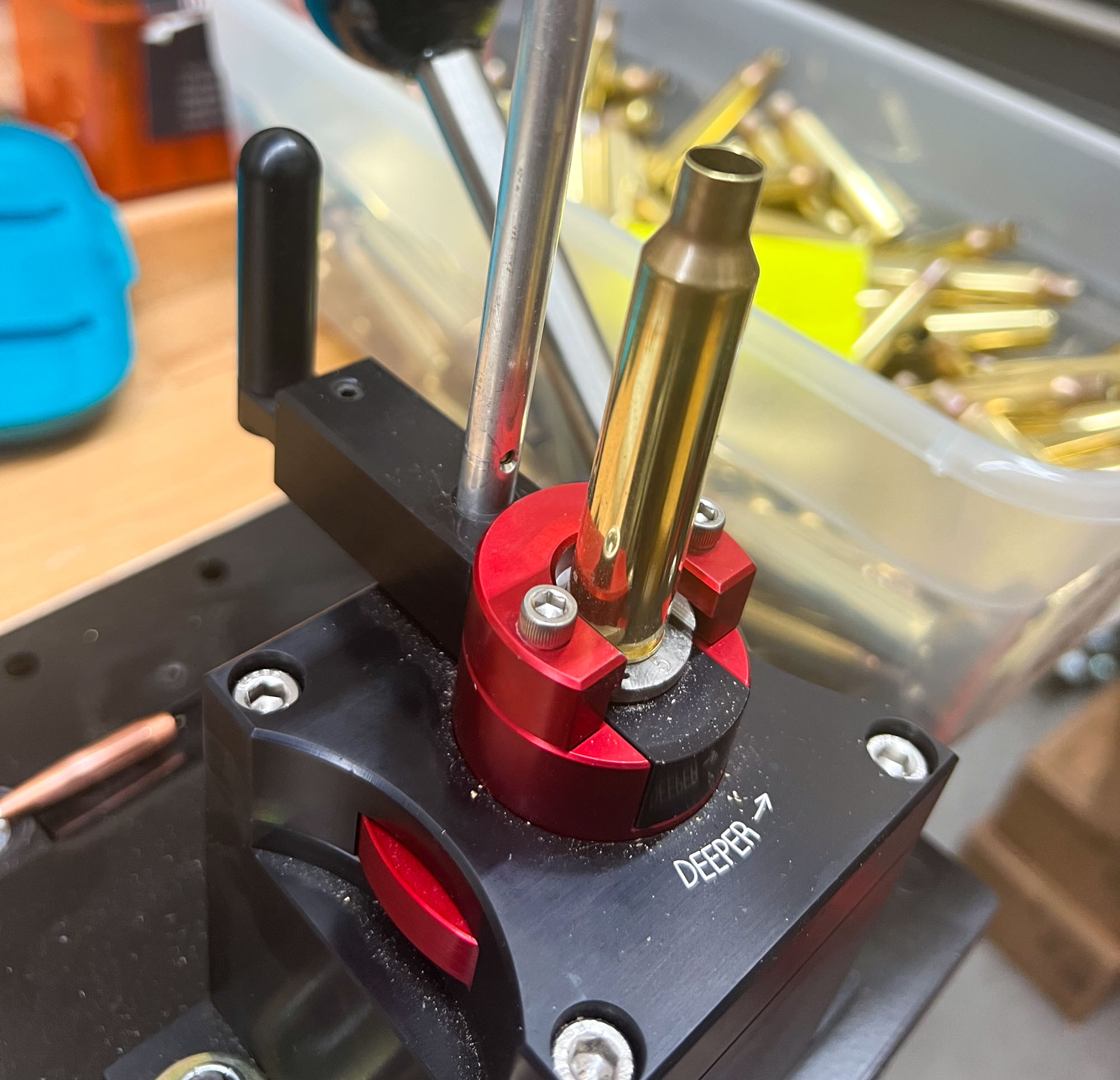
Reloading Equipment Used
To get peak accuracy from any handload you need to have consistent and concentric ammunition. In addition to the brass prep mentioned above, I used the following gear to craft my ammunition.
I primed my brass on a Primal Rights Competition Primer Seater. For speed and accuracy, no other priming system can match it. I can prime 100 cases in eight minutes on it, with all the primers seated to a precise depth, which the user can adjust. In the case of these .300 PRC rounds, I seated the 210Ms .003 inch below flush.
I threw my charges with my bank of three RCBS Matchmaster Powder Dispensers. They are capable of dispensing charges that are accurate to plus or minus a single kernel of powder and, once calibrated, are in perfect sync with each other. With three running at once it makes loading a couple hundred precision rifle rounds much quicker.
I seated the bullets in an Area 419 Zero Turret Press with a Redding Competition Seating Die. I replaced the seating stem that comes with the die with Redding’s VLD stem, which worked perfectly with the shape of the 230-grain A-Tips.
I don’t think I’ve ever loaded such concentric rounds. Measuring bullet runout on the ogive with a Sinclair Concentricity Gauge and Mitutoyo Digital Dial Indicator I had measurements as low as a fraction of a thousandth, with some maxing out at .002 inch, which is terrific.
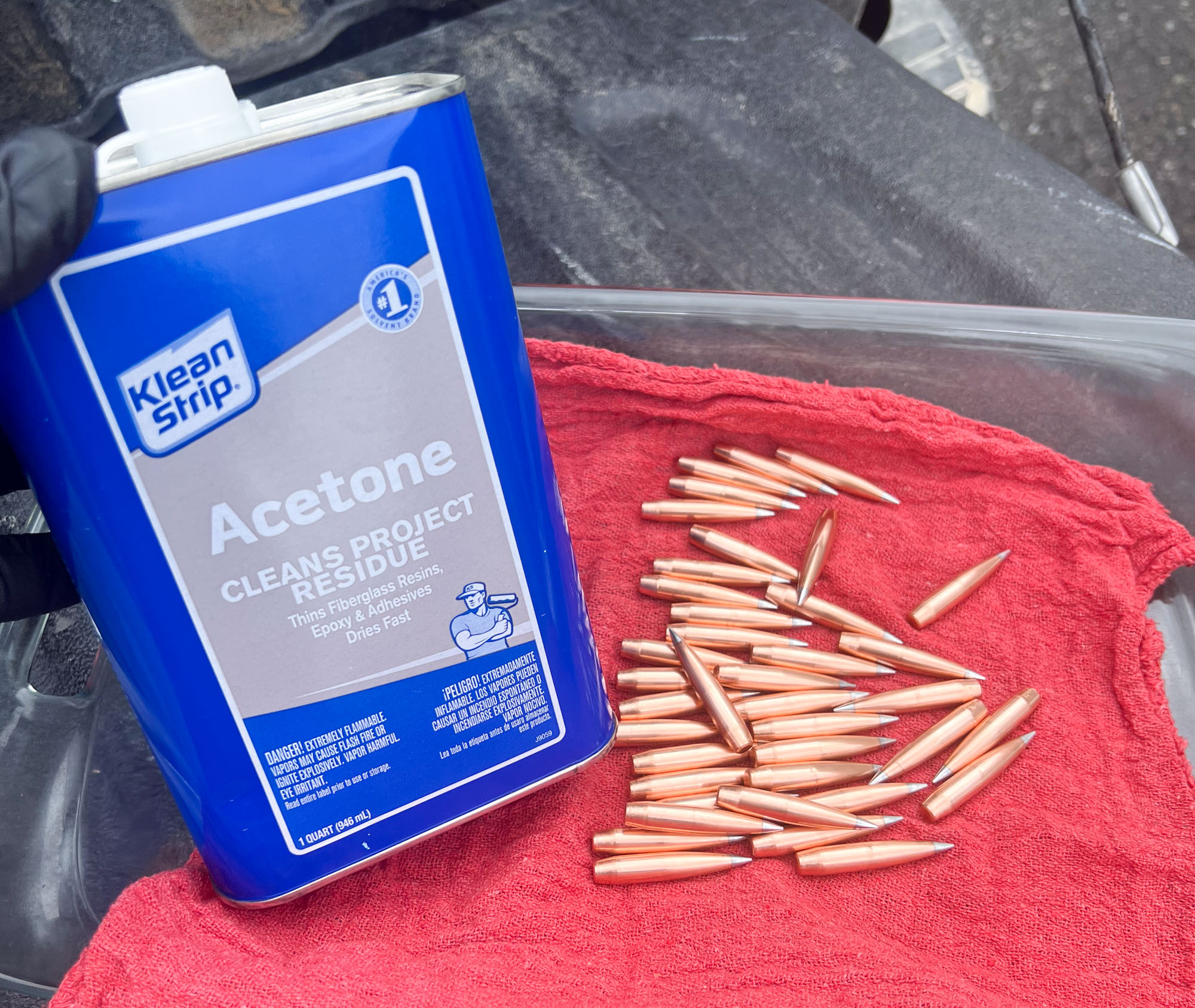
Cleaning the Bullets
Before seating the 230-grain A-Tips, I cleaned them using a technique Scott Seigmund told me about. This is necessary because A-Tips come from the factory with a coating of lube on them, which should be removed before loading.
Hornady ships the A-Tips with a felt Crown Royal-type bag you can use to wipe them down, but that gets old quick when you have dozens of rounds to load. Instead, spread out a lint-free shop rag and dump your bullets on it. Sprinkle acetone on the bullets and rag. Roll the rag like a burrito and grab both ends. Rock the bullets back and forth in the rag for a minute and that will remove the lubricant without damaging the projectiles.
Truing
Truing a load means different things to different shooters. I’m using it in the common, less-technical sense, meaning it is the process by which you get a ballistic calculator’s predicted results to line up with what you actually see in the real world.
Since I burned through so much of my unfired ADG brass and supply of bullets during load development, I didn’t have much cushion to work with.
The course of fire for the Nightforce ELR Steel Challenge has a maximum round count of 160 rounds and I had exactly 182 pieces of unfired brass left over. While I didn’t plan on shooting 160 rounds at the match, I didn’t want to tempt fate by rolling into Wyoming with a bare minimum of ammunition.
Shooting Groups at 100 and 600 Yards
I started by checking zero with three rounds at 100 yards, which hit dead center and measured .165 inches. I was shooting with Chris and Owen, who did the same thing. Happy with our results, we moved to the long-distance range.
We painted steel targets at 600 yards and got solutions from our Kestrels. At 2940 fps my elevation adjustment was 2.7 mils. I held for the 9 mph crosswind and shot a good group which indicated my calculated elevation correction was correct. So far, so good.
Chris’ and Owen’s loads were quite a bit slower than mine. Chris was pushing his 230s at 2830 fps while Owen was at 2885—an indication that we all had to go our own way to find what worked best in our rifles even though we were shooting the same components through barrels that were produced consecutively from the same batch of steel. They dialed their corrections and shot well at 600, too.
Stretching It to 1,000 Yards and Beyond
We had a handful of targets from 1,000 to 1,400 yards to shoot, and at 1,000 yards my data still looked good. I was running Applied Ballistics on a Kestrel 5700 Elite and Hornady’s 4DOF on my phone. In addition, I had a Sig Sauer Kilo10K-ABS rangefinding binocular with AB on board. I had to manually adjust the environmentals on the Sig 10K to accurately reflect the temperature, but once I did that all three units were basically in sync.
That said, I started to have difficulties on the 1,400-yard target. Chris and Owen were both spot on, but my shots weren’t grouping as tightly as they had been. My impacts were landing close to the target but not connecting. The only thing that took a hit was my confidence.
Had I gone through all this work only to end up with a rifle and load that dipped into mediocrity at longer distances—where the majority of the targets would be?
Desperation Time
Those thoughts were racing through my head as we packed our stuff to head home. I grabbed my rifle by the suppressor and felt it give a little, and my stomach lurched. I didn’t mention it to Chris and Owen, but told them I was going to do just a little more shooting and sent them on their way.
I don’t know when my suppressor had come loose, but it is one of the cardinal rules of long-range shooting to obsessively check your gear. In fact, Chris and I, who often partner during team shooting events, have a term for it. We call it doing a Macarena, as our hands go through a head-to-toe motion to make sure everything is in order on ourselves and our rifles before starting a stage.
After screwing the suppressor down tight, I reengaged the targets at 1,000 yards, 1,100 yards, and 1,400 yards. My shooting was tighter than a gnat’s nether regions. I was ready for Wyoming.
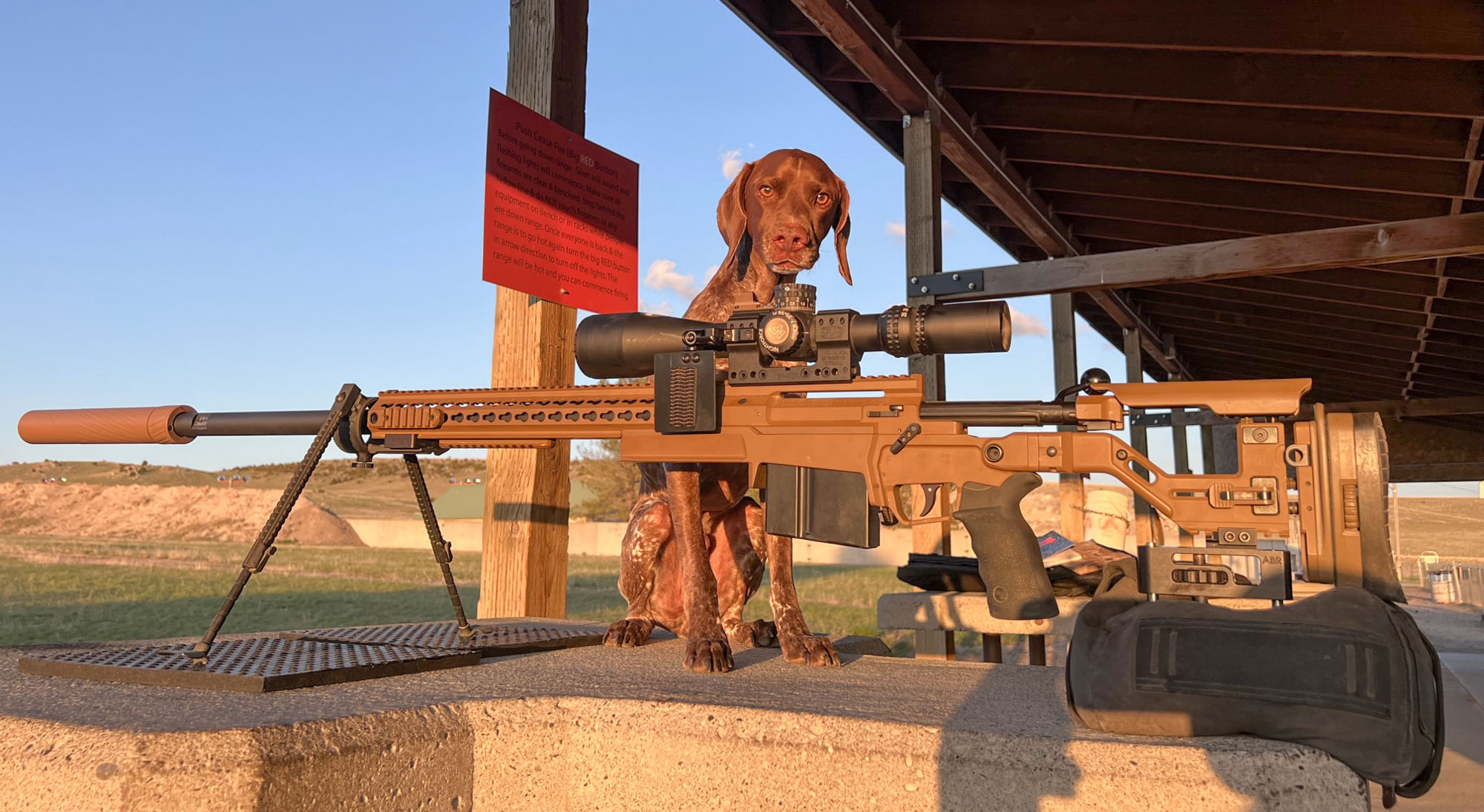
Running on Fumes
Expending those extra rounds was necessary but cost me some of my valuable remaining handloads. All told, I shot 53 rounds that day, and had fewer than 130 left for the match.
As a backup, I reloaded some of my once-fired brass, but as you might know, there’s usually a difference in velocities between virgin brass and cases that have been previously fired. I think this is because virgin brass expands more than fire-formed brass in the chamber—even if it has been fully resized, which mine was. So, some of the powder charge goes to that effort, resulting in reduced muzzle velocities with virgin brass.
To compensate, I dropped the powder charge in those resized rounds by two-tenths of a grain and hoped they’d shoot as close to 2940 fps as possible.
Final Thoughts
Despite spending a lot of time and resources preparing for the match, I was rolling into Glenrock with fewer rounds than was ideal. But there’s no shortcut when shooting something as difficult and competitive as ELR. If you leave anything to chance or otherwise half-ass it, you’re courting trouble.
It took me 373 rounds to get my rifle squared away, but in the end it was shooting groups averaging in the .5s (with a spread between .259 inches and .840 inches) and with SDs hovering right in the single digits or just above. For a .30-caliber magnum, that’s excellent performance—and good enough to win even the Nightforce ELR Steel Challenge.
As it turned out, my fellow shooters on the Accuracy International squad and I did shoot well. We also encountered some major difficulties along the way—which I will detail in the second installment of this story.