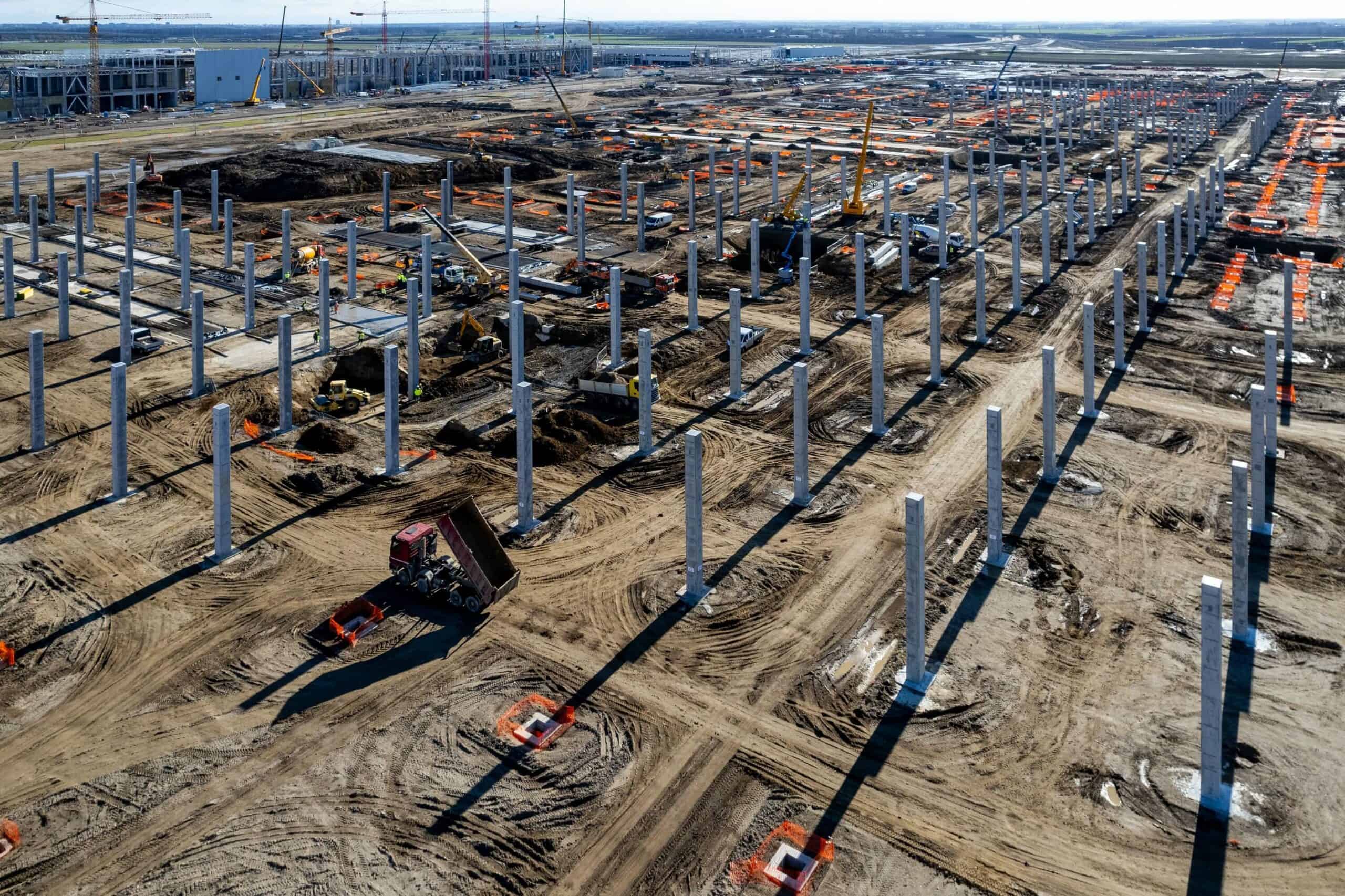
The BMW Group has a massive production network encompassing more than 30 factories all over the world. In 2022, it assembled nearly 2.4 million cars and over 200,000 motorcycles. However, the available capacity is not enough as the luxury brand is working hard at the new Debrecen plant in Hungary where it will begin to assemble Neue Klasse-based EVs from 2025.
In an interview with Automotive News, Member of the Board of Management of BMW AG, Production, Milan Nedeljković, said the company is actively searching for ways to reduce the time it takes to erect a new factory by as much as 40%. As it stands, BMW needs anywhere between 12 to 24 months to plan a new assembly factory and roughly the same amount of time to effectively build it.
The objective is to pretty much halve the time necessary for the planning stage and cut the entire plant construction process to as little as two years. The aforementioned Hungarian plant will be BMW’s first manufacturing facility to take advantage of Nvidia’s Omniverse platform to develop a digital equivalent of the factory. People involved in the factory planning can use the tech to test-fit tooling and integrate robots as well as improve ergonomics for the human workers.
It goes without saying that the longer it takes to build a plant, the more expensive it gets. According to industry experts cited by Automotive News, having a digital equivalent of a factory cuts the time by 20-30% and boosts quality by up to 20% while the resource consumption is optimized by 40%.
It’s not just about building new factories but also retooling existing ones to accommodate the production of EVs. BMW has already announced it wants electric vehicles to account for at least half of global annual sales by the end of the decade while MINI projects it will get there as early as 2025. The Oxford-based marque intends to go electric-only in 2030 when Rolls-Royce will also discontinue gasoline-fueled vehicles.